Why is the tracking of sterile goods in hospitals so important?
Hospitals rely on sterile goods, such as surgical and other sterilized instruments, being available in many areas, such as operating theaters, wards and A&E. The visibility of sterile goods is critical, enabling hospitals to treat patients quickly and efficiently, particularly those undergoing surgery.
The process of sterilizing equipment and surgical instruments for each operation has several steps. Typically, equipment is sterilized in a sterilization decontamination unit (SDU), then it is moved to local or remote storage locations before it is selected and transported to a theater preparation room ready for a procedure. Following a procedure, the items are transported back to the SDU and the cleaning and decontamination process starts again.
It is critical that the location of sterile goods is known to avoid delays and make this process as efficient as possible. This helps alleviate common challenges, such as hospital staff spending too much time locating sterile equipment, causing delays or even cancellations to operations, as well as putting increased pressure on sterile service reprocessing departments.
At Lyngsoe Systems, we have developed a GS1 approved tracking solution, Lyngsoe X-Tracking™, which uses RFID technology to provide real-time data on the location of sterile trays. Providing the visibility of sterile goods and other equipment through the tracking of these trays helps hospitals to improve operational efficiencies and support patient safety and care.
The benefits of tracking sterile goods for hospital and patients:
Benefits for hospitals
- Provides visibility of your sterile goods
- Assists the sterile service department with sterilized instrument and trolley tracking
- Saves time and reduces staff stress
- Improves operational efficiencies
- Improves patient flow
- Supports patient safety and infection control
Benefits for patients
- Reduces wait times, delays and cancellations
- Reduces the risk of infection or disease
- Improves patient care
- Improves the patient experience
How sterile goods tracking supports sterile service management systems
When staff in the sterile services department assemble sterilized equipment and surgical instruments to go to the operating theater or another hospital location, they link each device to a specific tray and case cart. The case carts are then used to transport the sterile goods from the SDU to their destination and back again after use.
X-Tracking™ tracks the case carts and trays, providing real-time data on their location, meaning that all sterile goods in circulation are easily located. The data is collected by ceiling-mounted RFID antennas, which have been installed at logistic choke points throughout the hospital, every time a tray or case cart passes through the point. Handheld RFID terminals are handling loading of case carts and can also be used by staff to manually register a tray or case cart location and update its status if required.
When the sterilized instruments are used in an operating theater, they are typically scanned by staff into a sterile service management system, such as T-DOC or Canexis – scanning is often enabled through reading laser-etched barcodes on single instruments.
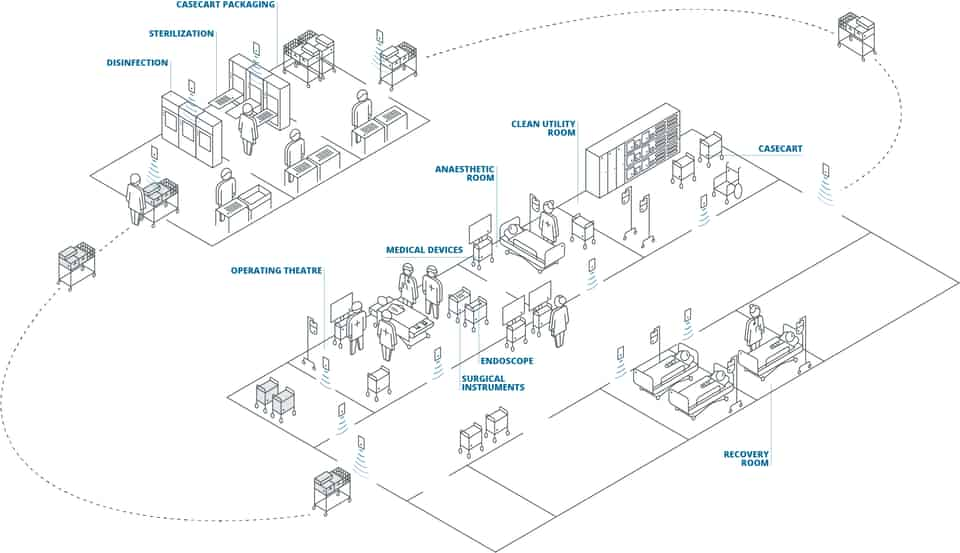
Streamline your sterilization process with sterile goods tracking
Our solution X-Tracking, will enhance your sterilization process, improve your operational efficiencies, and so much more - just check out the list of benefits:
- Supports your sterile goods management
- Improve operational efficiencies
- Provides real-time information that can be accessed from multiple devices anywhere, at any time
- Provides real-time information that can be accessed from multiple devices anywhere, at any time
- Visibility of flow helps manage pressure on the sterile service department
- Reduces patient wait times
- Avoid cancellation of planned operations
- Provides access to live and historic data that can be used to inform planning, budgeting and resource provision
- Supports patient care and patient safety initiatives
Unveil how others are streamlining their sterile goods management
Optimize your sterile goods workflow
Contact our team of experts to learn everything about sterile goods tracking.
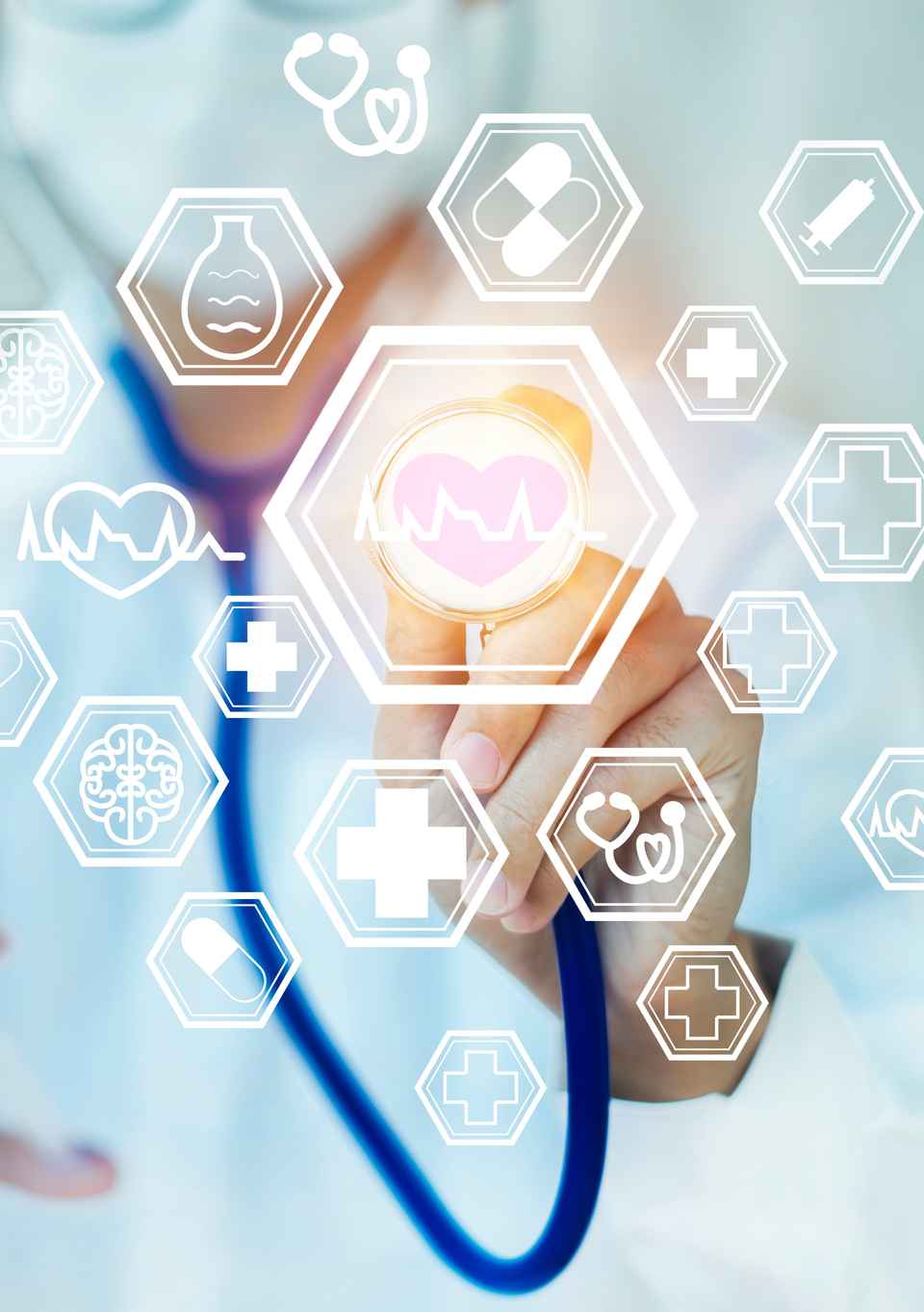
Explore other use cases for X-Tracking