The emergence of just-in-time manufacturing
The world of manufacturing is incredibly fast paced, so it stands to reason that the pursuit of efficiency is also fast moving. In many ways it’s inevitable that just-in-time manufacturing has continued to emerge as a highly effective strategy with many businesses now employing this approach due to its key benefits. The main motivation for using this method is to enhance efficiency and minimize waste by only producing goods as needed for the customer at that moment, hence the term, just-in-time. This practice leads to a reduction in overheads, such as inventory holding costs, however, it places more burden on manufacturers to accurately predict demand. One of the most recognisable names globally that is employing this strategy with great success is Toyota.
One technology that plays a crucial role in the success of just-in-time manufacturing is RFID. Here we’ll be looking at the impact of RFID in just-in-time manufacturing and how it contributes to the pursuit of greater efficiency.
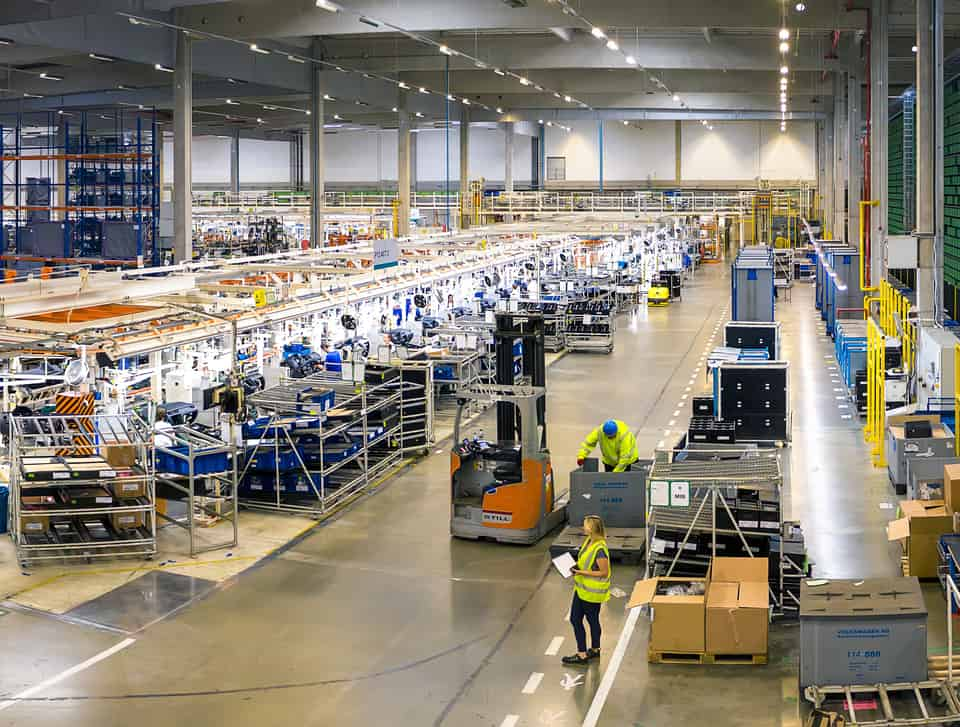
Unlocking just-in time manufacturing with the power of RFID
RFID technology involves the use of radio-frequency signals to transmit data between tags attached to an object and a reader. In just-in-time manufacturing, RFID is employed to track and manage the movement of materials and products throughout the production process.
Here are some of the key ways in which RFID contributes to boosting efficiency in just-in-time production:

Real-time inventory tracking
RFID enables real-time tracking of inventory levels, providing manufacturers with accurate and up-to-date information about the location and status of raw materials, work-in-progress and finished goods. This is particularly useful when complexity is high with regards to the BOM (Bill of Materials) – automated data capture ensures better control and visibility. This real-time visibility allows for better decision-making and helps prevent stockouts or overstock situations.
Streamlined production processes
With RFID, the production process can be automated and streamlined. As materials move through different stages of production, RFID tags attached to the items can automatically trigger the next step in the process. This reduces the need for manual intervention and minimizes the risk of errors, resulting in a more efficient production line and reduced variable cost.
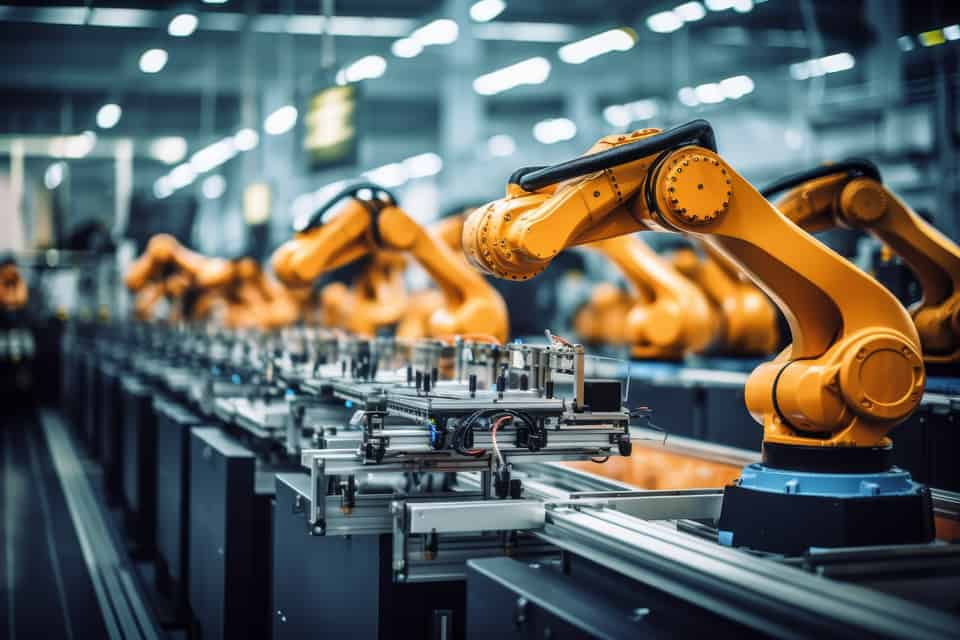
Enhanced supply chain visibility
RFID extends its benefits beyond the factory floor by enhancing visibility throughout the entire supply chain. Suppliers, manufacturers and distributors can all utilize RFID to monitor the movement of goods, coordinate shipments, and respond quickly to changes in demand. This end-to-end visibility is crucial for just-in-time manufacturing, where timely information is vital.
Improved quality control
RFID technology allows for the implementation of robust quality control measures. By tracking each component or product using RFID tags, manufacturers can quickly identify and address defects or issues, ensuring that only high-quality products move through the production process. This contributes to the overall efficiency of the manufacturing system, whether RFID is used on its own or in combination with existing MESH systems.
RFID drives just-in-time manufacturing strategies
In just-in-time manufacturing, where precision and efficiency are of prime importance, RFID technology is a powerful tool. From real-time inventory tracking to streamlined production processes and enhanced supply chain visibility, RFID contributes significantly to the success of just-in-time manufacturing strategies.
As businesses continue to embrace technology-driven solutions, the integration of RFID in just-in-time manufacturing will play a pivotal role in achieving operational excellence and maintaining a competitive edge in the ever-evolving manufacturing landscape.
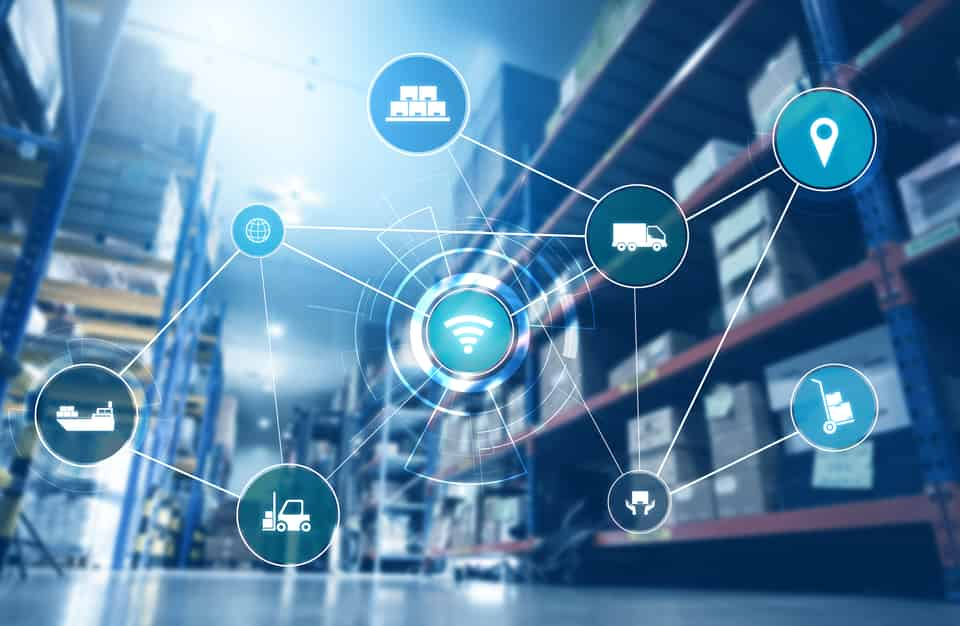
Explore Our Solutions